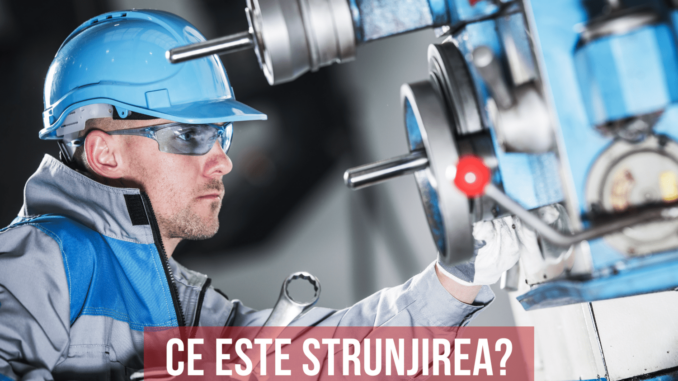
Strunjirea este una dintre cele mai vechi si fundamentale tehnici de prelucrare a metalelor, a parcurs un drum lung de la originile sale. Incepand ca o mestesugarie manuala, strunjirea a evoluat odata cu progresul tehnologic, devenind o componenta indispensabila a productiei industriale. Tranzitia de la strungurile manuale, operate prin forta umana sau mecanismele simple, la strungurile CNC (Control Numeric Computerizat), a reprezentat o revolutie in acest domeniu. Acest pas a permis realizarea unor lucrari mai complexe, cu o precizie si eficienta sporite, deschizand noi orizonturi pentru inovatie si design in industria prelucrarii metalelor. Astazi, strunjirea se afla in centrul multor procese de fabricatie, de la componentele auto minuscule la piesele mari pentru industria aerospatiala, evidentiind rolul sau crucial in evolutia tehnologica si inovatie.
Definitia si Aplicatiile Strunjirii
Strunjirea, definita ca un proces de prelucrare prin aschiere, joaca un rol esential in realizarea preciziei si calitatii superioare a pieselor. Procesul implica indepartarea stratului de material de pe o piesa rotativa fixata intr-un strung, utilizand unelte de taiere precise. Aceasta metoda este cruciala in multe industrii, inclusiv in sectoarele automotive si aerospatial, unde cerintele de precizie si fiabilitate sunt exceptional de ridicate. Prin strunjire, se pot obtine forme complexe si tolerante stricte, esentiale pentru asamblarea precisa si functionarea fiabila a componentelor in aceste domenii avansate.
Detalii si Aplicatii ale Diferitelor Tipuri de Strunjire
Strunjirea Longitudinala: Aceasta tehnica este adesea utilizata in fabricarea axelor sau a cilindrilor lungi. De exemplu, in industria automotive, strunjirea longitudinala este folosita pentru a produce axele de transmisie, unde suprafetele cilindrice trebuie sa fie extrem de netede si uniforme.
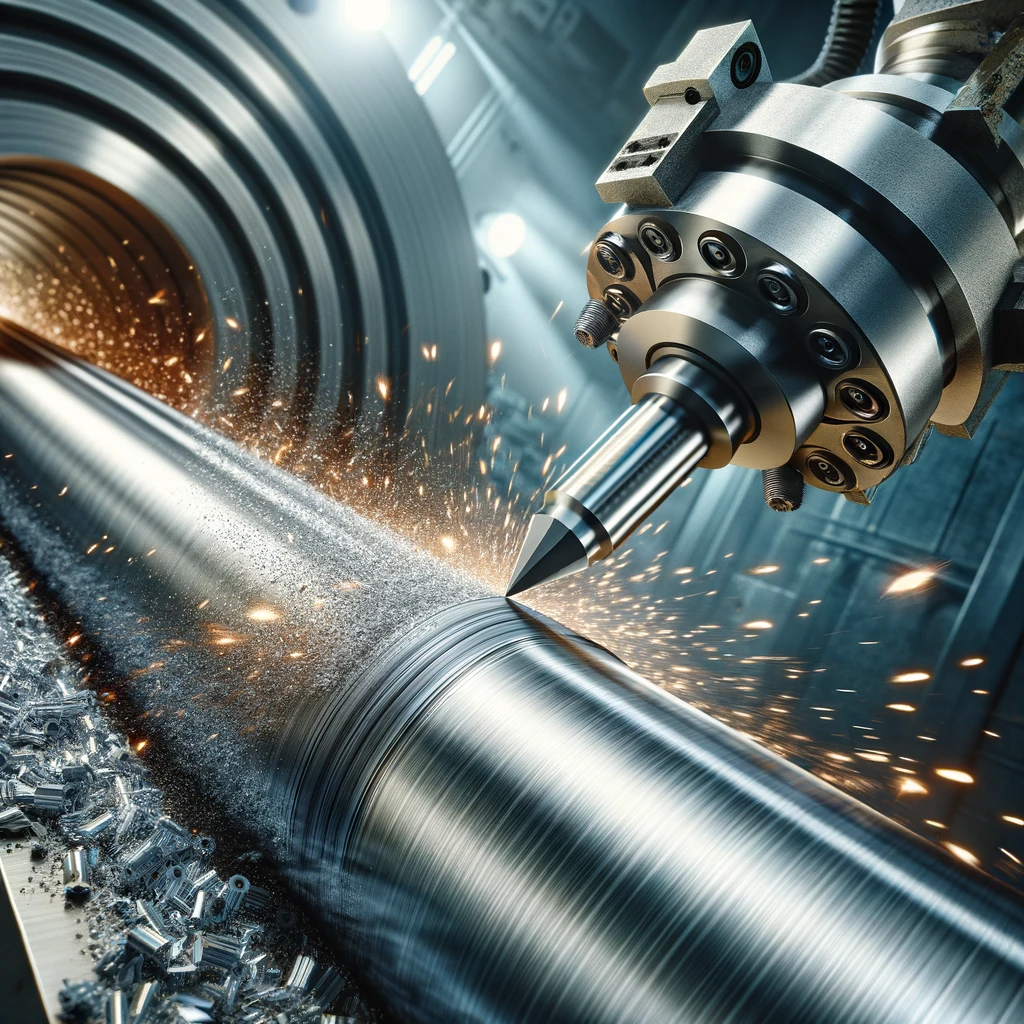
Strunjirea Frontala: Se aplica frecvent la finisarea fetelor de capat ale componentelor, cum ar fi capetele pistoanelor in motoarele cu combustie interna. Aceasta metoda asigura ca suprafetele de capat sunt plane si la un nivel precis de toleranta.
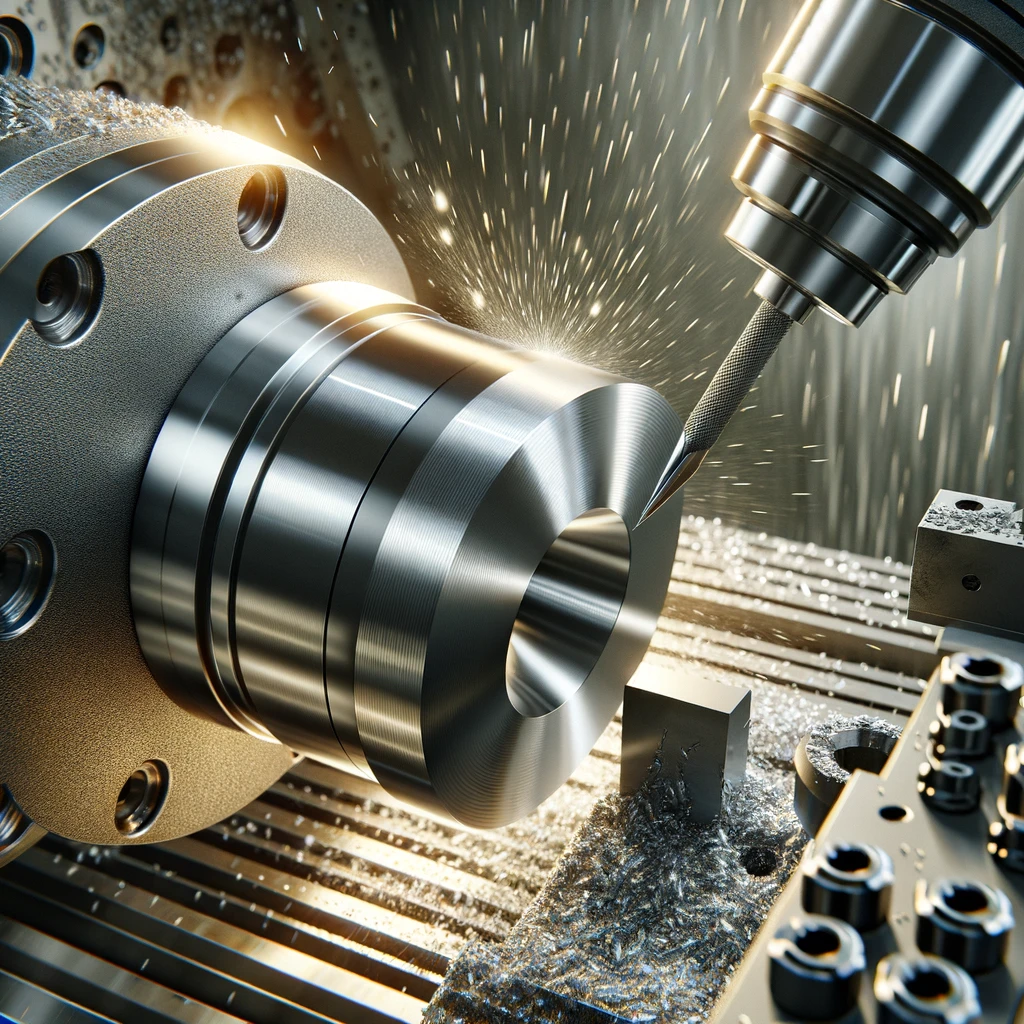
Strunjirea Conica: Este esentiala in crearea pieselor cu forme conice, cum ar fi partile conice ale arborelui cotit. Acuratetea unghiurilor conice este vitala pentru functionarea corecta a multor componente mecanice.
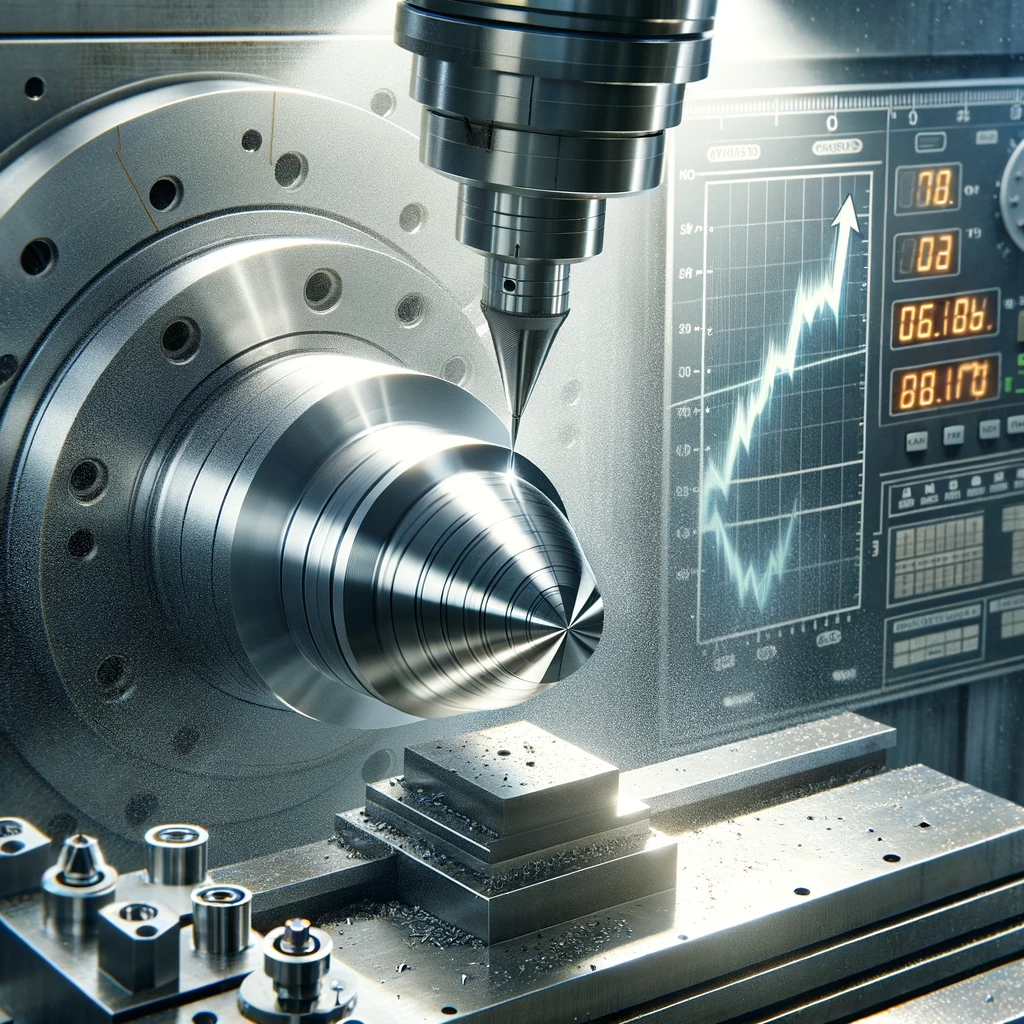
Strunjirea Filetului: Este folosita pentru a produce filete pe suruburi, bolturi si alte componente similare. In industria aerospatiala, de exemplu, filetele de precizie sunt esentiale pentru asigurarea integritatii structurale si fiabilitatii conexiunilor.
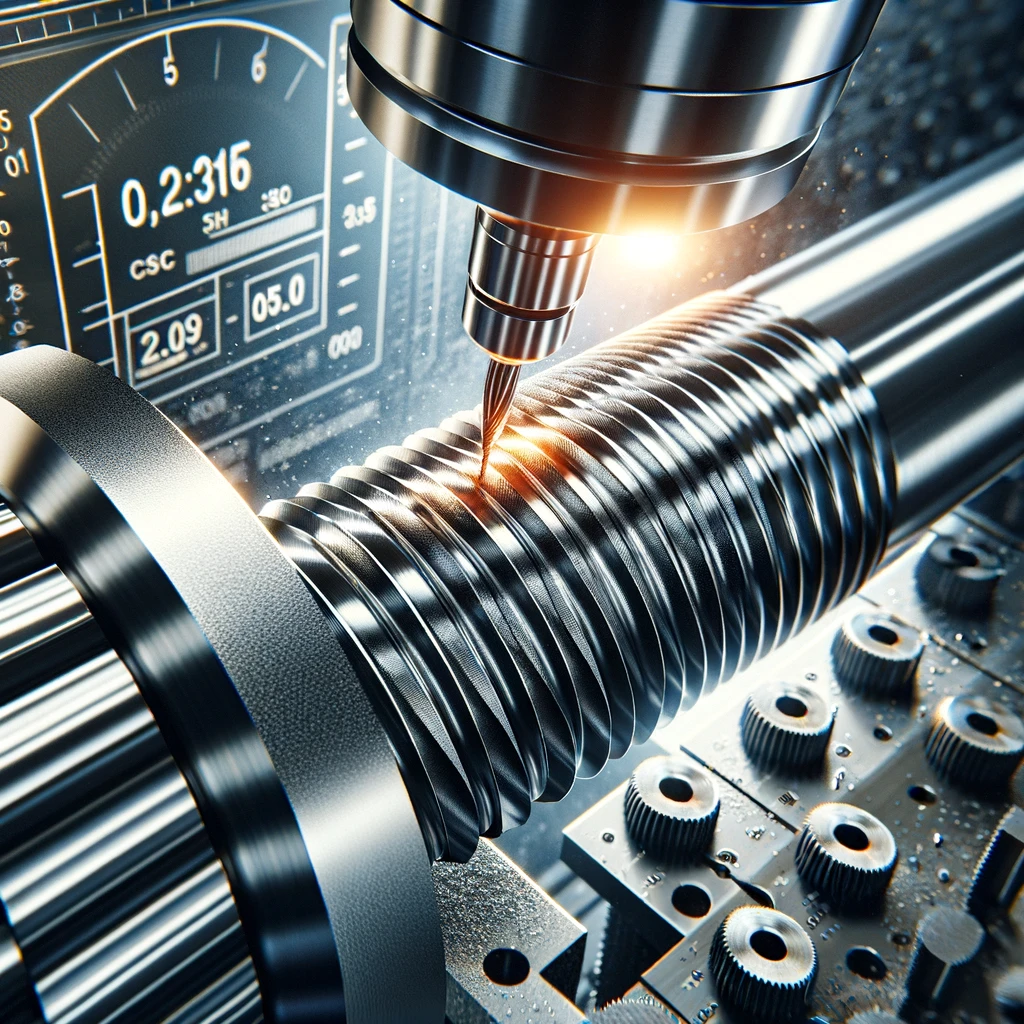
Fiecare dintre aceste tehnici de strunjire are aplicatii specifice si este aleasa pe baza cerintelor proiectului si specificatiilor piesei de prelucrat. Prin utilizarea acestor metode, se pot crea piese de o mare varietate si complexitate.
Selectarea Materialului si Sculei de Strunjire
Materiale Utilizate in Strunjire
Selectarea corecta a materialului pentru piesa de lucru este cruciala. Materialele frecvent utilizate includ:
Oteluri aliate si nealiate: Alegeri populare pentru rezistenta si durabilitatea lor.
Aluminiu: Preferat pentru usurinta de prelucrare si greutatea redusa.
Cupru si aliajele sale: Alese pentru conductivitatea lor electrica si termica.
Aliaje pe baza de nichel si titan: Folosite in aplicatii speciale pentru rezistenta lor la temperaturi inalte si coroziune.
Alegerea Cutitelor de Strung
Selectarea cutitului de strung este la fel de importanta. Factorii de luat in considerare includ:
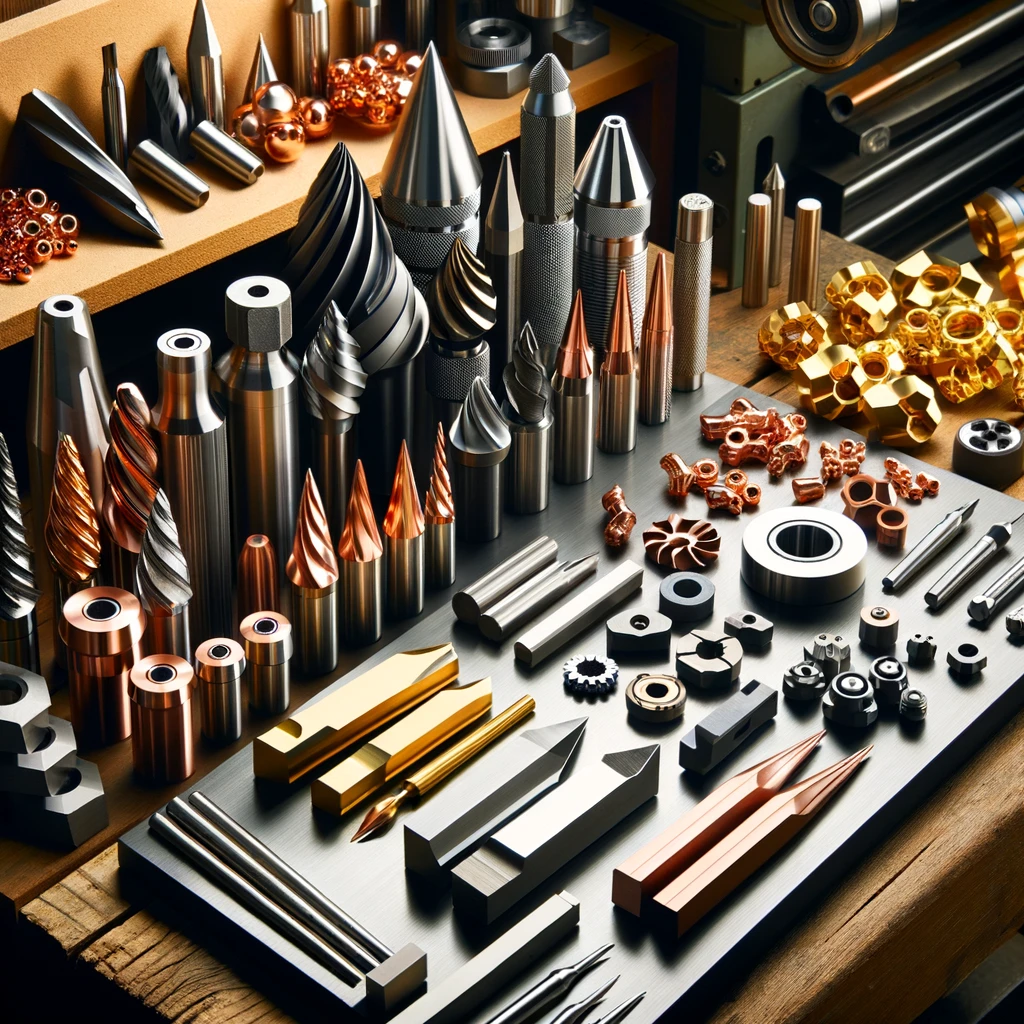
Materialul cutitului: Otel rapid, carburi metalice, cermet, fiecare avand avantaje specifice in termeni de rezistenta la uzura si duritate.
Geometria varfului: Unghiurile de aschiere si forma varfului sunt esentiale pentru eficienta prelucrarii si calitatea finisajului.
Alegerea potrivita a materialului si a sculei de strunjire influenteaza direct calitatea prelucrarii, eficienta si durata de viata a uneltelor.
Setarea Parametrilor de Taiere: Detalii si Aplicatii
In strunjire, setarea optima a parametrilor de taiere este esentiala pentru obtinerea unei prelucrari eficiente si de calitate. Aici sunt cateva exemple si studii de caz:
Viteza de Rotatie: Determina cat de repede se roteste piesa de lucru. Viteza prea mare poate genera caldura excesiva si poate duce la uzura rapida a cutitului, in timp ce o viteza prea mica poate reduce productivitatea. De exemplu, intr-un studiu de caz cu strunjirea otelului inoxidabil, o viteza optimizata a redus timpul de prelucrare cu 20%.
Avansul Cutitului: Este distanta pe care cutitul o parcurge intr-o singura rotatie a piesei. Un avans mic poate imbunatati finisajul, dar este mai lent, in timp ce un avans mare este mai rapid dar poate sa nu lase o suprafata la fel de fina. Un studiu de caz arata cum ajustarea avansului a imbunatatit finisajul suprafetelor aluminiului fara a sacrifica productivitatea.
Adancimea de Taiere: Afecteaza cantitatea de material indepartat in fiecare trecere a cutitului. Setari necorespunzatoare pot cauza defectiuni ale piesei sau pot deteriora scula de taiere. Intr-un caz, reglarea adancimii de taiere a redus tensiunile interne intr-o piesa de prelucrat, rezultand intr-o mai buna integritate structurala a componentei.
Pentru utilizatorii incepatori, este esential sa inceapa cu setari conservatoare si sa ajusteze parametrii treptat pe masura ce dobandesc experienta in interpretarea semnalelor procesului, cum ar fi culoarea aschiilor, zgomotul de taiere si uzura cutitului.
Executarea Procesului de Strunjire: Ghid Pas cu Pas
Fixarea Piesei: Initial, piesa de lucru este fixata ferm in mandrina strungului. Este crucial sa se asigure ca fixarea este sigura pentru a preveni orice deplasare in timpul prelucrarii.
Exemplu: Inainte de a fixa o piesa de aluminiu, este verificata pentru a ne asigura ca nu exista imperfectiuni care ar putea afecta strunjirea.
Sfat: Utilizati gabarite pentru a alinia piesa rapid si corect.
Setarea Cutitului de Strung: Cutitul de strung este apoi montat si aliniat la inaltimea corespunzatoare axei piesei pentru a asigura taierea precisa.
Exemplu: Pentru strunjirea otelului, se poate alege un cutit de strung din carburi metalice pentru o durabilitate mai mare.
Sfat: Asigurati-va ca cutitul este ascutit si reglat la inaltimea corecta.
Selectarea Parametrilor de Taiere: Viteza de rotatie, avansul si adancimea de taiere sunt setate in functie de materialul piesei si tipul de operatiune de strunjire.
Exemplu: La strunjirea fina a unui ax de precizie, se alege o viteza de rotatie mai mica si un avans fin pentru a obtine un finisaj neted.
Sfat: Incepeti cu setari conservatoare si ajustati pe masura ce observati cum reactioneaza piesa.
Procesul de Strunjire: Masina este pornita, iar cutitul de strung incepe sa indeparteze materialul conform parametrilor selectati.
Monitorizarea Procesului: Procesul este monitorizat atent pentru a detecta abateri sau probleme.
Exemplu: In timpul strunjirii unei piese de cupru, operatorul trebuie sa fie atent la caldura generata si sa ajusteze lichidul de racire corespunzator.
Sfat: Fiti atenti la sunetul masinii si la aspectul aschiilor pentru a identifica problemele.
Inspectarea si Finisarea Piesei. Verificarea Finala: Dupa finalizarea strunjirii, piesa este evaluata pentru a verifica daca dimensiunile si finisajul corespund specificatiilor.
Exemplu: Dupa strunjirea unui fus, se masoara diametrul cu un subler pentru a confirma ca se incadreaza in tolerantele cerute.
Sfat: Folositi echipament de masurare calibrat pentru a verifica precizia.
Practicile optime includ utilizarea lichidelor de racire pentru a mentine temperatura scazuta, verificarea periodica a uzurii sculei si ajustarea parametrilor daca este necesar pentru a mentine calitatea.
Probleme Comune si Solutii in Strunjire
Abateri de la Tolerante
Problema: Dimensiunile piesei nu respecta specificatiile tehnice.
Solutii: Verificati corectitudinea setarilor de pe strung.
Re-calibrarea echipamentului de masurare.
Asigurati-va ca piesa este fixata corespunzator si ca nu se deplaseaza in timpul prelucrarii.
Uzura Prematura a Uneltelor
Problema: Sculele de taiere se uzeaza rapid, afectand calitatea prelucrarii.
Solutii: Selectati cutitele potrivite pentru materialul prelucrat.
Ajustati viteza de rotatie si avansul in functie de recomandarile pentru materialul si cutitul folosit.
Utilizati lichide de racire pentru a reduce caldura generata.
Vibratii in Timpul Strunjirii
Problema: Vibratiile cauzeaza un finisaj superficial necorespunzator.
Solutii: Asigurati-va ca toate componentele masinii sunt stranse si ca masina este nivelata.
Utilizati cutite cu tija anti-vibratie si reduceti lungimea libera a piesei de lucru.
Abordarea acestor probleme comune va imbunatati calitatea strunjirii si va prelungi viata sculelor.
Tehnologii Avansate in Strunjire
Masinile de strunjire cu CNC sunt dotate cu capabilitati avansate, permitand programarea detaliata a proceselor de strunjire, care includ schimbari complexe de unelte, ajustarea parametrilor de taiere si optimizarea traiectoriilor de taiere. Aceasta duce la scaderea timpilor de pregatire si la cresterea eficientei generale.
Automatizarea a extins posibilitatile de utilizare a strungurilor CNC, cu sisteme de alimentare automata a pieselor si evacuare a produselor finite, precum si cu software care poate anticipa si corecta erorile in timp real. Aceste sisteme pot functiona neintrerupt, chiar si in afara orelor de lucru normale, sporind productia si reducand nevoia de supraveghere constanta.
Monitorizarea avansata si analiza datelor colectate de la strungurile CNC ajuta la optimizarea continua a proceselor de strunjire, prin identificarea tendintelor, prevenirea defectelor si prelungirea duratei de viata a uneltelor. Aceste progrese tehnologice contribuie semnificativ la imbunatatirea calitatii pieselor produse si la eficientizarea productiei.
Concluzie
Strunjirea ramane una dintre cele mai esentiale si versatile tehnici de prelucrare in industria moderna, esentiala in productia de componente cu tolerante stricte si finisaje de calitate. Avansurile in tehnologia CNC si automatizare augureaza o eficienta si o precizie crescute, deschizand drumul spre o productie mai inteligenta si mai conectata. Viitorul strunjirii se profileaza a fi unul in care integrarea cu sistemele de fabricatie aditiva si procesele digitale va duce la inovatii si optimizari care vor transforma continuu peisajul manufacturier.
Intrebari frecvente (FAQs) despre Strunjirea in metal
- Ce este strunjirea? Strunjirea este un proces de prelucrare prin aschiere unde un cutit de strung indeparteaza material dintr-o piesa rotativa pentru a-i conferi forma si dimensiunile specificate.
- Cum se clasifica strunjirea? Strunjirea se clasifica dupa miscarea cutitului: longitudinala pentru suprafete cilindrice, frontala pentru suprafete plane, conica pentru crearea conurilor si filetare pentru realizarea filetelor.
- Ce materiale se folosesc in strunjire? Materialele utilizate includ oteluri aliate si nealiate, aluminiu, cupru si aliaje pe baza de nichel sau titan.
- Ce rol au parametrii de taiere in strunjire? Parametrii de taiere influenteaza eficienta, precizia si durata de viata a sculei, fiind esentiali pentru calitatea finala a piesei.
- Cum afecteaza automatizarea strunjirea? Automatizarea imbunatateste precizia si eficienta prin utilizarea strungurilor CNC, care permit prelucrari complexe si rapide.
- Ce sunt strungurile CNC? Strungurile CNC sunt masini de strunjire automate controlate de un computer, care permit realizarea precisa a pieselor complexe.
- Cum se alege cutitul de strung corect? Selectia cutitului de strung se bazeaza pe materialul de prelucrat si tipul operatiei de strunjire, tinand cont de materialul cutitului si geometria varfului.
- Ce sunt vibratiile in strunjire si cum se reduc? Vibratiile sunt oscilatii care pot afecta calitatea suprafetei; reducerea lor se face prin ajustarea parametrilor si folosirea sculelor cu amortizare.
- Cum se executa strunjirea filetului? Strunjirea filetului presupune folosirea unui cutit special pentru a crea filete de-a lungul axei piesei.
- Care este viitorul tehnologiei de strunjire? Tehnologia se indreapta spre integrarea cu procese digitale si automatizarea completa, crescand eficienta si reducand costurile.